Carbon capture essential for scaling net-zero concrete – global cement producer
This text is part of our new package on frontier climate technologies. Check out our Q&A on CCS.
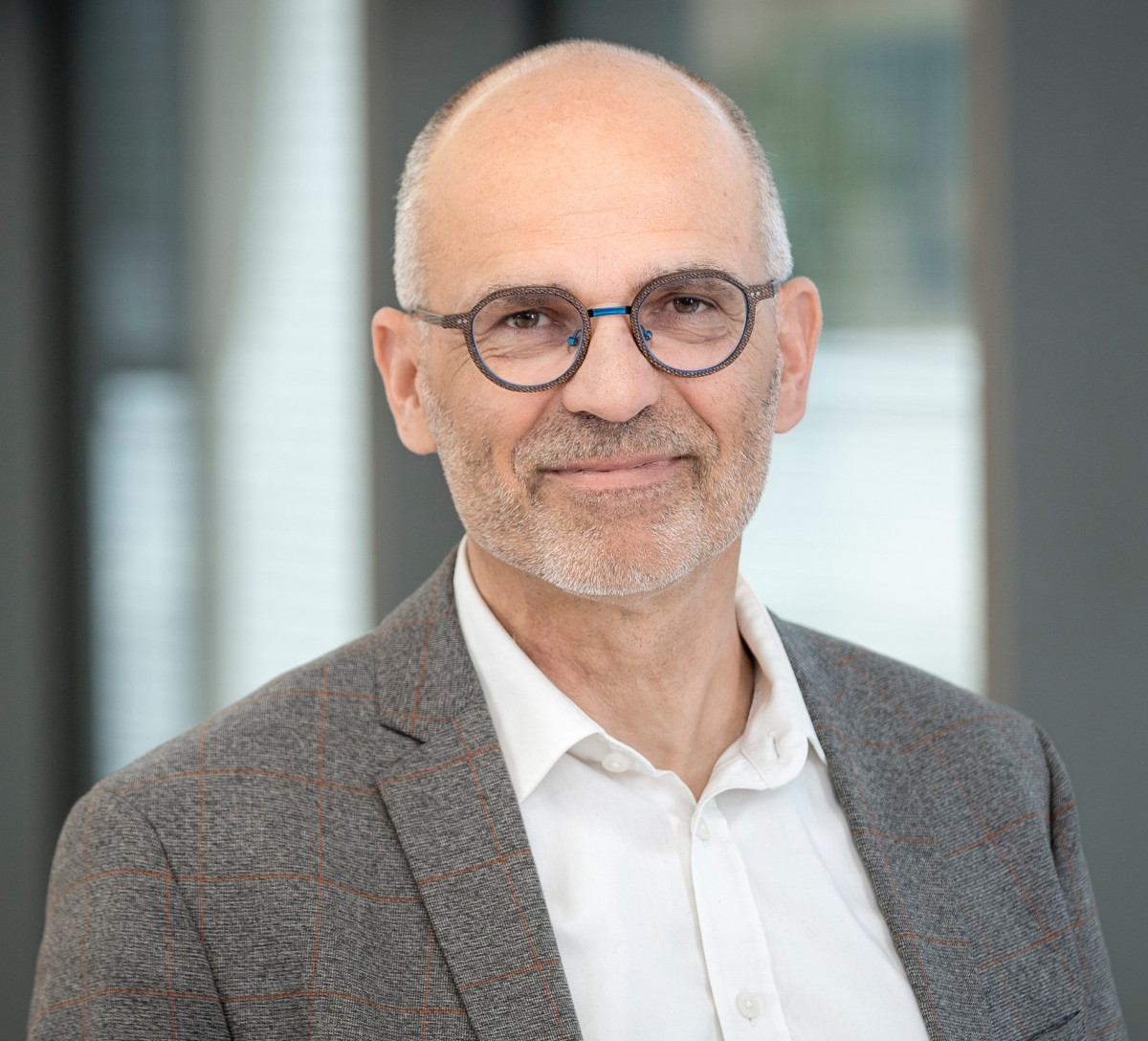
Clean Energy Wire: Many experts say that carbon capture and storage (CCS) technologies should mainly be used for hard-to-abate sectors, where it is difficult to lower carbon intensity. What role does CCS play in the cement industry?
Jan Theulen: First of all, the cement industry is a large emitter. We have substantial emissions because there is a lot of concrete being used in society, and its production comes with emissions that are unavoidable: There is a large portion of process-related CO2 that is coming from the raw materials. We are using calcium carbonate which is then transformed to calcium oxide. This process releases CO2. The calcium oxide is part of clinker. From grinding the clinker, you get cement – the “glue” in concrete.
We try to use as little clinker as possible in cement. We take a lot of measures to substitute clinker with other cementitious materials like fly ash, blast-furnace slag or other pozzolans. And we are making good progress in continuously reducing our carbon footprint.
Another source of emissions are the fuels used in the furnaces. We will further reduce our carbon footprint by replacing fossil fuels with alternative fuels coming from non-recyclable waste with biogenic content. But there will be a remaining fraction of CO2 emissions which we cannot avoid. For that fraction CCUS is the only solution to reach net zero.
Would you say that it is even possible to produce cement in a climate neutral way?
Yes, definitely. There are already binders on the market which are carbon neutral. You can make a carbon neutral binder from waste ashes. You do not call it cement because there is no clinker in it. It works in a somewhat similar way – but it does not come with the same strength properties as normal cement. Also, the materials needed for carbon neutral binders are scarce.
Therefore, we have to come up with other solutions to decarbonize large volumes of cement and concrete. In that sense, CCS is the only possibility to produce net-zero cement and concrete. First, you avoid emissions as I explained. Then you capture the remaining CO2. Our project in Brevik will be the first to deliver net-zero cement and concrete to the market in large volumes. CCS can be scaled up to large volumes. That is the big difference to other concepts on the market.
From a technological point of perspective, it is impossible to have a 100 percent capture rate of CO2. Are you offsetting the fraction of emissions that you cannot capture to live up to the claim of carbon neutrality?
No, we are not using offsetting. The biogenic fraction of the waste that we co-process in our cement kilns is quite considerable. This leads to biogenic CO2 molecules in the flue gas which are already ‘neutral.’ Nevertheless, we catch them.
If you catch 95 percent of the CO2 in flue gas, but that flue gas already contains ten percent ‘neutral’ CO2 from biogenic content, then you stand at minus five percent at the end. You could even produce a slightly carbon negative clinker. That is not offsetting. Offsetting is for example planting trees. We do not think that this can be a solution for our industry. We need to solve our own issue with our own installations.
There is a demand for biomass from many sectors. With the huge cement industry that we have today, is there enough biogenic material?
We are not using pure, virgin biomass in general. Pure biomass like wood chips or pure byproducts from the agricultural sector are not our feedstock. Instead, in our plants we use waste-derived fuels, such as municipal waste: The recyclable part has already been recycled. But a fraction remains that is not economically possible to recycle. That is a mix of some plastics, some textiles, some organic waste, some small wood pieces, maybe a little bit of paper. The mixture usually has 40-50 percent biogenic content. Our kilns can operate with this mixture since we are using it for thermal purposes. Other sectors have different needs, so our feedstock needs are not in conflict with other demands.
Do any active carbon capture projects in the cement production exist today?
Until today, mainly pilot projects have been realised on different scales. There is no carbon capture project with storage connected to it in the cement industry yet. In that sense the project in Brevik will be the first in the world. There are projects where some CO2 is captured either for demonstration purposes or for utilisation. We are also working on such a project in Germany to capture CO2 and to make food-grade CO2 for the market. But these are the smaller volumes.
It is not like turning the knob and up it will go. We still have a lot of work to do to run it in an optimised way.
Heidelberg Materials is a huge company in the cement business and at the forefront of today's implementation of CCS. Where do you stand regarding the maturity of the carbon capture technology?
We feel very confident about the technology because we started testing it already ten years ago at our Brevik plant in Norway. We have learnt a lot, we have built this unit, we have seen other facilities of the same technology at other power stations. We feel very confident.
But it is not like turning the knob and up it will go. We still have a lot of work to do to run it in an optimised way. It is a journey. We will learn a lot and we will learn from any challenges along the way.
Isn't that a rather big bet on technologies that are not yet mature if you plan with CCS to become climate neutral in your production, or maybe even across all operations of your company?
I would not put it like this. It is a new technology for us in the cement business. We need to master implementation in our sector, but the amine capture technology has been successfully applied on multiple installations around the world for many years. We are now testing our own cement-based oxyfuel technology. In terms of technology, we are not jumping to the Mars. It is really manageable. We have to make a business case out of it and get it done in an affordable way. That is the next stage we are working on.
What are technological challenges you are still facing?
A carbon capture unit requires substantial energy. That obviously comes with costs and resource needs. We are working to optimise this.
At Brevik we have done it by using a lot of waste heat from the plant. We will only capture 50 percent of the CO2 because this capture rate is in balance with the available waste heat from our own clinker production process. That means we do not need to burn natural gas to operate the desorber of the amine capture system. We are looking now for further methodologies to scale it up. The next projects will treat 100 percent of the flue gas and then capture around 95 percent. We try to limit the energy demand and that is where the big learnings come from.
The second most important learning is about the purity of the CO2 that you capture. You must meet certain specifications so that the pipeline does not run into troubles with erosion or corrosion.
You also plan a carbon capture project in Germany. Here, you want to sell the captured carbon for use. Does that mean you also sell the responsibility for the emissions?
No. In our project in Lengfurt with Linde we will capture CO2 and purify it to a food grade quality. Linde then sells it to their customers. The typical customer from Linde will not store the CO2, they use it for cooling, for sparkling water or similar purposes. Of course, once it is used, it is released again, meaning CO2 is emitted. For that we still have to submit allowances in the EU Emissions Trading System. We are responsible and we pay. Only when you store the CO2 permanently you are released from that obligation.
Aside from the technological part, you also spoke about the economic challenges. What does Heidelberg Materials need to ramp up the CCS technology?
A couple of things. We are working hard to bring the capture cost down with a more efficient capture technology. That is where we as engineers work on.
An important part in the value chain is the transport and storage of CO2. Particularly for the transport of CO2 it is important that a pipeline infrastructure will be developed in Europe. It is not always possible to transport the CO2 by ship as it is done in Brevik which is located at the coast. For many cement plants and other industrial emitters, it is way more efficient to create a CO2 pipeline infrastructure. This is something that must be initiated and promoted by governments because the infrastructure is created for multiple users and not only for us.
In addition, governments should incentivise buying sustainable products. We are selling the world’s first carbon captured net-zero cement, evoZero. This product makes net-zero construction possible.
Then we need a higher ETS price as a driver of the CCS ramp-up. Last but not least, our industry increasingly pays for ETS allowances, as free allowances are phased out from 2026 onward. The revenues from CO2 pricing should be re-injected to support the industry to decarbonise.
Is there money to be made in climate friendly cement made with CCUS?
Yes, absolutely. We will not market a product without a viable business case. If a developer wants permission for constructing a building, they might have to indicate for example how it looks like, what the energy efficiency is, but also how much the embodied carbon is, which represents the carbons emissions released during the lifecycle of building materials. Concrete is responsible for 50 percent of the embodied carbon of the building. If they can replace the cement by using evoZero, they can halve of the embodied carbon.
The cement price is only one to two percent of the building costs. Therefore, the cost of the building will just go up a bit but the embodied carbon has dropped a lot. The product brings value to those who are willing to commit to such building materials.
You also sell lots of traditionally produced cement. Will you have different prices for different products? Will there be different markets?
Yes. We have evoZero which is net-zero. We also have evoBuild with a reduced carbon footprint, but not zero. And then we have the classical cements. It is about providing value for users of each product. Only if the end user is happy with the technical and environmental performance then there is a good match between the user and us as a supplier.
How much more does carbon neutral cement cost than the regular cement?
Pricing for cement and concrete typically varies depending on classification and suitability for specific applications. evoZero is a unique product with unique properties that will be sold at a completely new price point.
In Germany, the efforts to reform the regulation to push CCS in the last parliament failed and must now be taken up again. What does that mean for Heidelberg Materials in Germany and in Europe?
The efforts are indeed delayed, because the German government broke apart before the law was adopted. Overall, the understanding in the German society and the German politics is that without CCS it will be very difficult for Germany to reach climate neutrality by 2045. That is accepted, particularly for the hard-to-abate sectors like cement, steel and waste to energy. We are confident that this will be solved relatively soon by the new government. We do think there is a broad consensus that CCS should be done.
And we welcome the societal and political debate about CCS, because people have to support it. You cannot just implement it top down. This dialogue will come in every country. And that is fine. It is a healthy dialogue. As long as at the end of dialogue, action is being taken.
Where do you see the role of the European market in the world? Is that a very important market also from a regulatory standpoint?
Yes, the EU adopted the Industrial Carbon Management Strategy and the Net Zero Industry Act, which mandates CO2 storages. The EU has a very good framework to facilitate CCS in principle. There are different member states which are clearly leading the way, like Denmark, the Netherlands or Sweden. But Germany is definitely following that track as well.